How to Inspect Your Trailer Floor for Hidden Damage
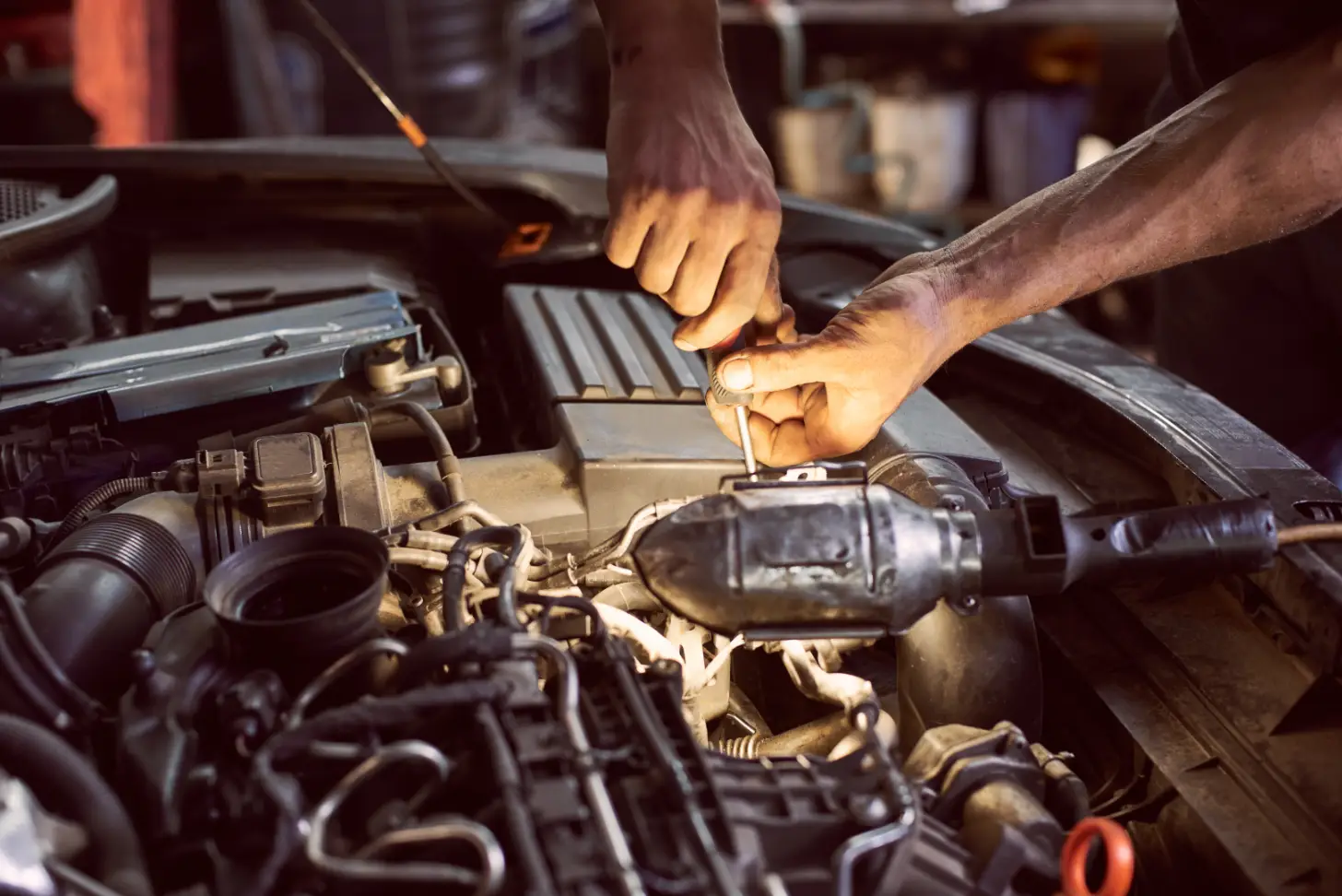
A trailer floor might look solid at first glance, but hidden damage can lurk beneath the surface, waiting to cause serious problems. Whether you're hauling heavy freight, livestock, or construction materials, a weak or deteriorating floor can compromise safety, reduce cargo stability, and lead to costly structural repairs. Over time, moisture, weight stress, and unnoticed wear can cause wooden planks to rot, aluminum to weaken, or steel components to corrode, putting both the trailer and its cargo at risk.
At first, minor cracks, soft spots, or small patches of rust may not seem like urgent issues. The trailer still holds weight, and there’s no immediate sign of collapse. But here’s the reality: hidden damage in the floor can rapidly worsen, leading to sagging sections, loose fasteners, and even complete floor failure under heavy loads. Catching these problems early through thorough inspections is the key to avoiding expensive repairs, lost cargo, or even a serious accident on the road.
The Importance of a Strong Trailer Floor
The floor of a trailer is one of its most critical components, providing structural support for cargo, equipment, and even vehicle movement. A strong, well-maintained floor ensures that weight is evenly distributed, prevents cargo from shifting during transport, and reduces the risk of stress fractures in the trailer frame.
Heavy-duty trailers rely on different types of flooring materials, each with its own potential failure points. Wooden floors can develop rot, warping, or cracks, while aluminum and steel floors are prone to corrosion, rust buildup, and fatigue fractures. Regardless of the material, regular inspections and proper maintenance are essential to keeping the trailer roadworthy and protecting valuable cargo.
Ignoring trailer floor damage doesn’t just affect durability—it can also create serious liability risks. If a weak section of flooring gives way under load, it can lead to shifting cargo, load instability, and dangerous on-road conditions. Structural failure can also compromise tie-down anchor points, causing secured loads to break free and shift dangerously during transit.
How Hidden Damage Develops in Trailer Floors
A trailer floor doesn’t fail overnight—damage happens gradually due to constant weight stress, exposure to moisture, and unnoticed small cracks or leaks. One of the biggest threats to trailer floors is water damage, which can seep in through roof leaks, improperly sealed edges, or pooling water from condensation. Over time, wood flooring absorbs moisture, leading to soft spots, fungal growth, and rotting planks.
Metal floors aren’t immune to damage either. Steel trailer floors are vulnerable to rust and corrosion, especially in regions where road salt, humidity, or exposure to chemicals speeds up deterioration. Aluminum floors, while resistant to rust, can suffer from metal fatigue, causing the surface to become thin, brittle, and prone to cracking under heavy loads.
Another common issue is floor fastener failure. Over time, screws, bolts, and welds that hold the flooring in place can loosen due to road vibrations, repeated cargo loading, and expansion from temperature changes. A loose fastener can create gaps in the floor, which can widen with repeated stress, eventually leading to entire sections of flooring becoming unstable.
How to Perform a Thorough Trailer Floor Inspection
Regular trailer floor inspections are crucial for catching hidden damage before it leads to a major failure. The best time to inspect is before loading cargo, after long trips, or whenever you notice unusual noises, sagging, or movement in the floor panels.
A proper inspection starts with a full visual check of the floor’s surface. Look for cracks, warping, soft spots, or visible signs of damage. If you notice discoloration, peeling coatings, or water stains, this could indicate moisture penetration, which weakens the floor over time. Using a flashlight and a mirror, check underneath the trailer for signs of rust, rot, or gaps in the subfloor.
For wooden floors, pressing firmly on different areas with your foot can help identify soft spots or weakened planks. If the wood flexes too much, it could mean the material has lost its strength and needs to be replaced. Wooden flooring should also be inspected for splinters, surface cracking, and signs of insect damage, which can compromise its load-bearing capacity.
Metal floors should be checked for corrosion, cracks, and weld integrity. Running your hands over the surface can help detect uneven textures, weak spots, or small stress fractures that might not be visible. If rust is present, tap the area with a rubber mallet—if the sound is hollow or flakes of metal fall away, the corrosion has weakened the structure.
Don’t forget to inspect fasteners, tie-down points, and joints. Loose bolts or missing screws can cause floor panels to shift, leading to gaps or movement under heavy loads. Check the edges of the trailer floor, where water intrusion and stress tend to cause the most damage.
If the trailer has a rubber or coated floor, look for bubbles, peeling, or soft spots underneath the covering. Damage beneath a protective layer can often go unnoticed until it’s too late.
The Cost of Ignoring Trailer Floor Damage
Ignoring trailer floor maintenance can lead to serious structural failures, putting both cargo and drivers at risk. A weakened floor can collapse under heavy loads, damaging the axles, suspension, and frame. The cost of replacing a trailer floor can be significantly higher than routine maintenance, especially if additional repairs to the frame or substructure are required.
In the worst cases, trailer floors that fail during transport can lead to on-road accidents, spilled cargo, or even DOT violations. Many states have strict load securement laws, and a compromised floor could result in fines, penalties, or insurance issues if a load shifts unexpectedly.
How to Prevent Trailer Floor Damage
Preventing trailer floor deterioration starts with regular cleaning, sealing, and protective treatments. Keeping the floor dry and free of standing water helps prevent rot, rust, and corrosion. Applying sealants, rust inhibitors, or moisture-resistant coatings adds an extra layer of protection, especially for wood and steel flooring.
Routine maintenance should include tightening fasteners, checking welds, and ensuring cargo is evenly distributed to prevent unnecessary strain on certain areas of the floor. Keeping the trailer stored in a dry, covered area also reduces exposure to rain, snow, and fluctuating temperatures, which can weaken the flooring over time.
Scheduling professional inspections and repairs ensures that hidden damage is caught early before it leads to costly replacements. Trained mechanics can detect small fractures, compromised welds, and early-stage rust that might not be visible to the untrained eye.
Trust Dog House Trailer Repair for Expert Floor Inspections and Repairs
If you suspect trailer floor damage or want to ensure that your flooring is structurally sound, trust Dog House Trailer Repair in Richmond, VA. Our experienced team specializes in trailer floor inspections, repairs, and preventive maintenance, ensuring that your flooring remains durable, secure, and compliant with load safety standards.
A small crack, soft spot, or minor rust patch might not seem urgent today, but ignoring it could lead to costly structural failures tomorrow. Don’t take the risk—schedule a professional trailer floor inspection today and keep your cargo and equipment protected.