Factory vs. Aftermarket Bottom Rail Repairs: Which Is the Better Option?
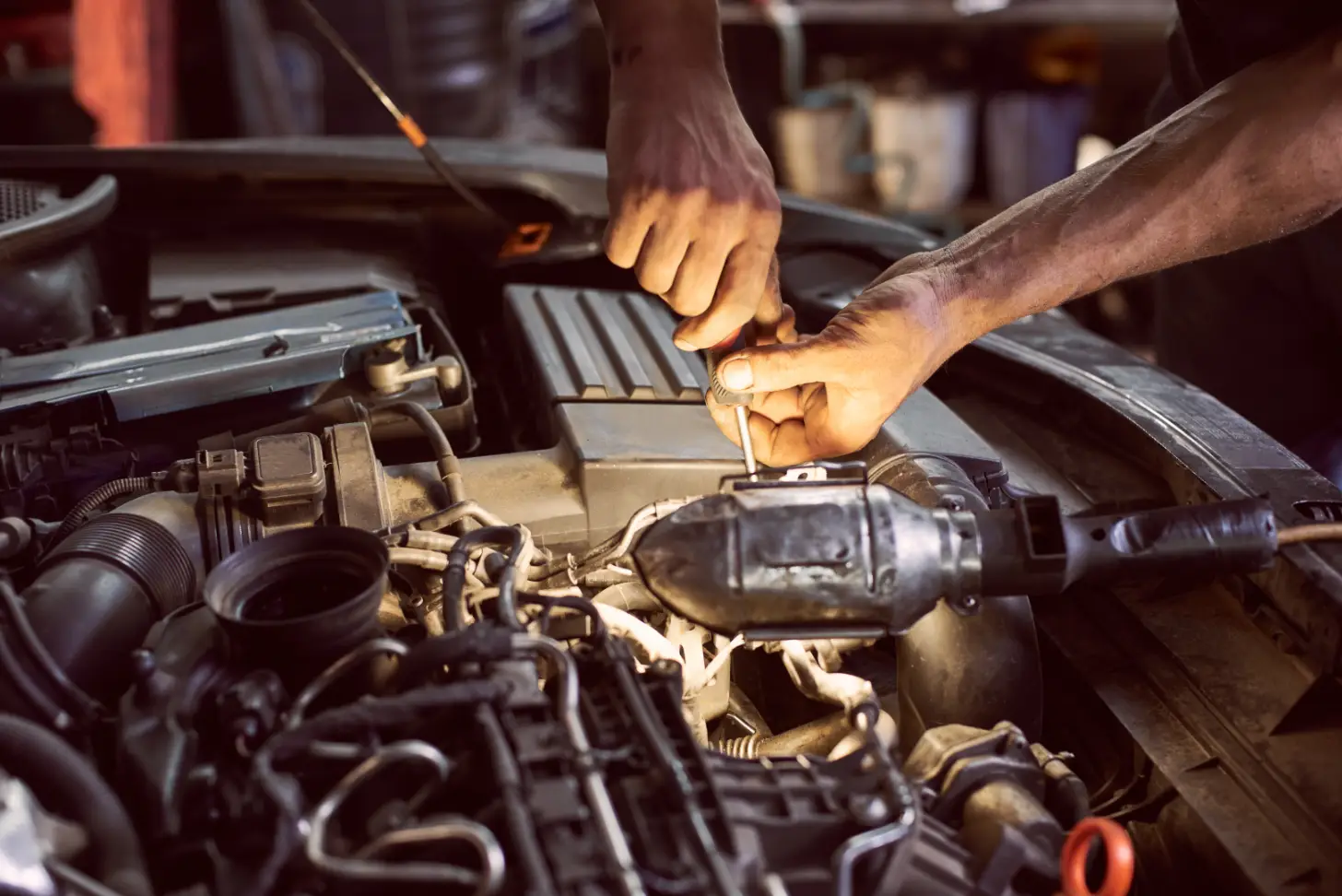
Introduction
The bottom rail of a trailer or semi-truck plays a crucial role in structural integrity, cargo protection, and long-term durability. Over time, bottom rails can suffer damage from corrosion, impact, and wear, requiring repair or replacement. When this happens, truck owners must decide between factory (OEM) replacement rails or aftermarket alternatives.
Choosing the right option affects repair costs, structural strength, and resale value. Understanding the differences between factory and aftermarket bottom rail repairs ensures that fleets make the best investment for long-term performance and compliance.
What Is a Bottom Rail and Why Is It Important?
The bottom rail is a structural support component that runs along the lower frame of a trailer, box truck, or semi-truck chassis. It helps to reinforce the cargo area, prevent frame flex, and protect against road debris and impact damage.
A damaged bottom rail can lead to:
- Weakened structural integrity, increasing the risk of trailer failure.
- Gaps and leaks, expose cargo to moisture, dust, and external elements.
- Reduced resale value, as buyers inspect for signs of frame repairs.
- DOT compliance issues, since a severely damaged frame may fail inspections.
Factory (OEM) Bottom Rail Repairs
Factory (OEM) bottom rails are direct replacements from the original manufacturer, designed to match the truck’s frame dimensions, materials, and load capacity. These parts ensure that repairs restore original specifications and performance.
Advantages of Factory Bottom Rail Repairs
Factory replacement rails are designed for exact fitment, reducing the need for custom modifications or additional fabrication. This results in easier installation, proper alignment, and fewer compatibility issues.
OEM bottom rails meet factory engineering standards, ensuring consistent strength, durability, and corrosion resistance. These parts are tested and certified to withstand heavy loads and long-haul conditions.
Using factory parts helps maintain the resale value of a trailer or truck, as buyers prefer OEM repairs over aftermarket modifications. Keeping the frame as close to original specifications as possible enhances marketability and trade-in value.
Since OEM bottom rails match the truck’s original design, there’s a lower risk of modifications affecting structural integrity or load distribution. Using factory parts ensures that the truck remains compliant with DOT and FMCSA regulations.
Disadvantages of Factory Bottom Rail Repairs
OEM replacement parts tend to be more expensive than aftermarket options, making repairs less cost-effective for older trucks or minor damage.
Factory parts are often subject to long lead times if they are out of stock or need to be ordered from the manufacturer. For fleet operators with urgent repairs, waiting for OEM parts can mean lost revenue due to downtime.
OEM bottom rails provide limited customization, making it difficult to enhance corrosion resistance, weight reduction, or added reinforcement beyond the factory design.
Aftermarket Bottom Rail Repairs
Aftermarket bottom rails are manufactured by third-party companies, offering an alternative to factory replacement parts. These parts often vary in materials, design, and cost, depending on the manufacturer.
Advantages of Aftermarket Bottom Rail Repairs
Aftermarket rails are typically more affordable than OEM replacements, helping fleet operators reduce repair costs while maintaining structural integrity.
Many aftermarket manufacturers offer enhanced materials, such as reinforced aluminum or corrosion-resistant coatings, which may provide better longevity than standard factory parts.
Aftermarket bottom rails are often readily available, reducing lead times and allowing for faster repairs and less downtime. Fleet operators who need to get trucks back on the road quickly may find aftermarket parts more practical.
Some aftermarket manufacturers offer custom-fabricated bottom rails, allowing truck owners to reinforce high-stress areas, improve aerodynamics, or reduce weight. This flexibility can enhance performance and durability beyond factory specifications.
Disadvantages of Aftermarket Bottom Rail Repairs
Not all aftermarket rails match the exact specifications of the original part. Variations in dimensions, thickness, or material composition may require modifications or additional welding, increasing installation time and labor costs.
Some aftermarket bottom rails are made with lower-quality materials that may not meet OEM strength and durability standards. Choosing a low-cost, poorly manufactured replacement can lead to premature failure and costly re-repairs.
Using non-OEM replacement parts may lower resale value, as buyers and fleet managers prefer factory-certified repairs. Trucks and trailers with aftermarket structural modifications may require additional inspection or recertification before resale.
Which Option Is Best for Your Fleet?
The choice between factory and aftermarket bottom rail repairs depends on budget, time constraints, and long-term fleet goals.
Factory bottom rail replacements are best for fleets that:
- Want to preserve resale value with manufacturer-approved repairs.
- Require exact fitment and engineering standards.
- Have time to wait for OEM part availability.
Aftermarket bottom rail replacements are ideal for:
- Cost-conscious repairs on older or heavily used trucks.
- Fleets needing quick turnaround due to limited downtime.
- Trucks operating in harsh conditions that require customized reinforcement.
For high-quality repairs, fleet operators should work with experienced technicians who understand how bottom rail modifications affect structural integrity and compliance.
How to Prevent Bottom Rail Damage
While bottom rails naturally wear over time, following preventative maintenance strategies can help extend their lifespan:
- Inspect rails regularly for cracks, corrosion, and impact damage. Catching minor issues early prevents costly repairs.
- Wash the undercarriage frequently, especially after driving on salted roads or in corrosive environments.
- Reinforce high-wear areas with protective coatings or additional support brackets.
- Use load distribution techniques to minimize stress on the frame and prevent warping.
- Repair minor dents or scrapes immediately, as exposed metal can lead to rapid rust formation.
Conclusion
Choosing between factory and aftermarket bottom rail repairs depends on budget, durability requirements, and long-term fleet goals. Factory replacements provide exact fitment and maintain resale value, while aftermarket options offer cost savings, faster availability, and customization possibilities.
By working with skilled repair professionals and prioritizing preventative maintenance, fleet operators can ensure long-lasting repairs and optimal trailer performance.
For professional bottom rail repair and structural maintenance in Richmond, VA, contact Dog House Trailer Repair today.